Pri prispôsobovaní kovových výrobkov je výber správnej metódy spracovania rozhodujúci pre kvalitu, cenu a dodaciu lehotu produktu. Existujú rôzne bežné metódy na prispôsobenie kovov.Tu je niekoľko bežne používaných metód prispôsobenia kovov:
1.CNC obrábanie:
CNC (Computer Numerical Control) obrábanie je metóda presného rezania a spracovania kovov pomocou počítačom riadených obrábacích strojov.Využitím predprogramovaných inštrukcií umožňuje CNC obrábanie vysoko presné a efektívne prispôsobenie kovových dielov, vhodné pre výrobky so zložitými tvarmi a presnými požiadavkami.
Výhody:
Vysoká presnosť a presnosť
Široká škála kompatibilných materiálov
Vhodné pre zložité tvary a zložité vzory
Efektívne pre malé aj veľké výrobné série
Nevýhody:
Vyššie náklady na počiatočné nastavenie
Dlhší čas výroby pre zložité návrhy
Obmedzené na subtraktívnu výrobu (odstraňovanie materiálu)
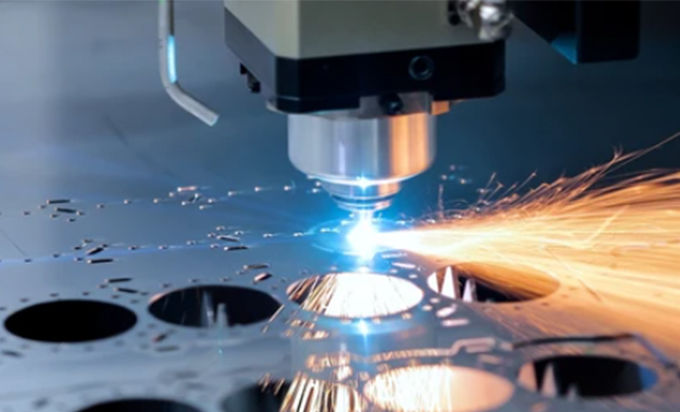
2. Frézovanie a sústruženie:
Frézovanie a sústruženie zahŕňa odrezávanie kovového materiálu z obrobkov pomocou nástrojov na obrábacom zariadení, aby sa dosiahli prispôsobené tvary a veľkosti.Frézovanie je vhodné na obrábanie plochých a zložitých plôch, zatiaľ čo sústruženie sa používa na valcové obrobky.
Výhody:
Presné a presné opracovanie
Všestranné pre rôzne tvary a veľkosti
Vhodné pre prototypy aj veľkosériovú výrobu
Široká škála kompatibilných materiálov
Nevýhody:
Dlhší čas obrábania pri zložitých návrhoch
Vyššie náklady na vybavenie a údržbu
Obmedzené na rotačné alebo symetrické časti pri sústružení
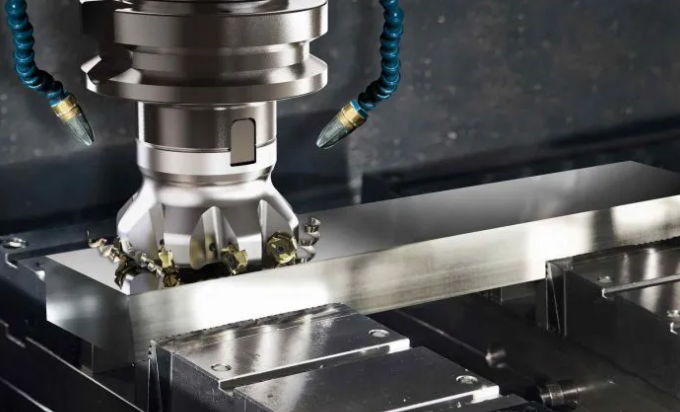
3.3D tlač:
Technológia 3D tlače umožňuje prispôsobenie kovových dielov vrstvením materiálov.Roztavením alebo stuhnutím kovových práškov je možné priamo tlačiť zložité kovové časti, čo ponúka výhody rýchlosti, flexibility a prispôsobenia.
Výhody:
Vysoko prispôsobiteľné a zložité návrhy
Rýchle prototypovanie a skrátená doba prípravy
Menšie plytvanie materiálom v porovnaní s tradičnými metódami
Vhodné pre malosériovú výrobu
Nevýhody:
Obmedzené materiálové možnosti v porovnaní s tradičnými metódami
Nižšia pevnosť a odolnosť v porovnaní s niektorými tradičnými metódami
Nižšia rýchlosť výroby väčších dielov
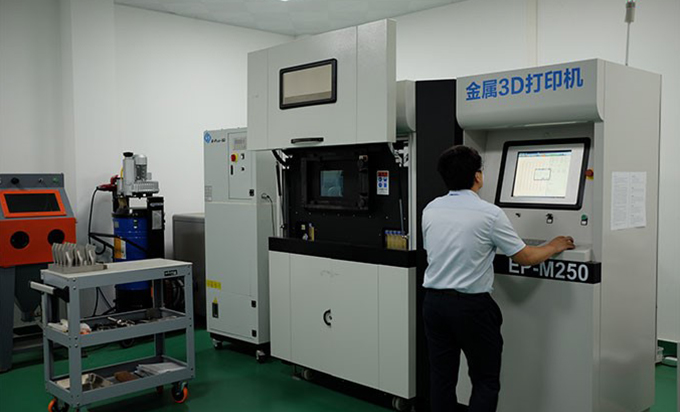
4. Laserové rezanie:
Laserové rezanie je metóda, ktorá využíva vysokoenergetický laserový lúč na roztavenie, odparovanie alebo spaľovanie kovových materiálov na účely rezania.Laserové rezanie ponúka výhody, ako je vysoká presnosť, rýchlosť, bezkontaktnosť a minimálna deformácia, vďaka čomu je vhodné na prispôsobenie širokej škály kovových častí a konštrukcií.
Výhody:
Vysoká presnosť a jemné detaily
Vysoká rýchlosť rezania
Bezkontaktný proces, minimalizujúci deformáciu materiálu
Vhodné pre rôzne kovy a hrúbky
Nevýhody:
Obmedzené na 2D rezacie profily
Vyššie náklady na vybavenie a údržbu
Pre hladké okraje môže byť potrebné dodatočné dodatočné spracovanie
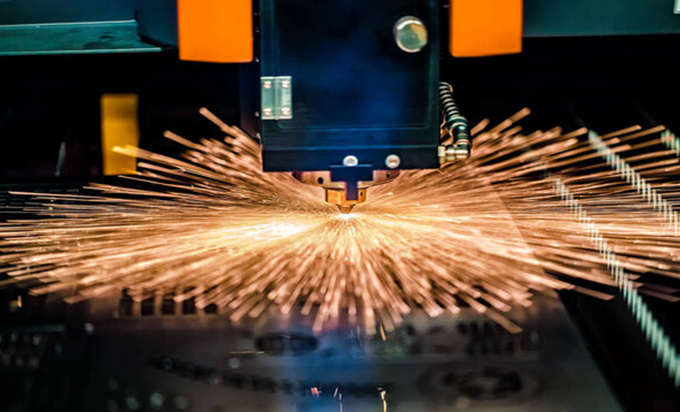
5.Pečiatkovaniea formovanie:
Razenie a tvarovanie zahŕňa vyvíjanie tlaku na kovové materiály, aby sa tvarovali do požadovaných foriem.Procesy lisovania za studena alebo lisovania za tepla možno použiť na dosiahnutie zákazkových kovových dielov a komponentov so zložitými tvarmi a vysokou presnosťou.
Výhody:
Vysoká rýchlosť výroby pre veľké množstvá
Nákladovo efektívne pre opakujúce sa návrhy
Vhodné pre zložité tvary a úzke tolerancie
Zvýšená pevnosť a odolnosť materiálu
Nevýhody:
Vyššie počiatočné náklady na nástroje
Obmedzené na konkrétne tvary a veľkosti
Nie je ideálne pre prototypy alebo malé výrobné série
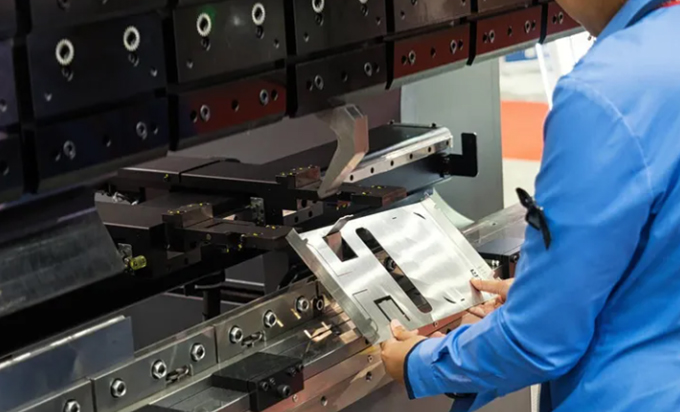
6.Odlievanie pod tlakom:
Tlakové liatie je proces, pri ktorom sa roztavený kov vstrekuje do formy pod vysokým tlakom, aby rýchlo stuhol a vytvoril požadovaný tvar.Medzi hlavné kroky patrí príprava formy, tavenie kovu, vstrekovanie, chladenie a vyberanie z formy.
Výhody:
Vysoká presnosť: Tlakové liatie môže produkovať diely so zložitými tvarmi, zložitými detailmi a presnými rozmermi, čím sa zabezpečí konzistentnosť a vysoká presnosť.
Vysoká efektivita výroby: Tlakové liatie je vhodné pre hromadnú výrobu s rýchlym vstrekovaním a rýchlym chladením, čo umožňuje vysoké výstupné rýchlosti.
Pevnosť a trvanlivosť: Diely odliate pod tlakom typicky vykazujú vynikajúce mechanické vlastnosti vrátane vysokej pevnosti, tuhosti a odolnosti proti korózii.
Nevýhody:
Vysoké náklady: Odlievanie pod tlakom vyžaduje výrobu špeciálnych kovových foriem, ktoré môžu byť drahé z hľadiska nákladov na výrobu foriem a prípravu.
Obmedzený výber materiálov: Tlakové liatie je primárne použiteľné pre kovy s nízkou teplotou topenia, ako sú zliatiny hliníka, zliatiny zinku a zliatiny horčíka.Je menej vhodný pre kovy s vysokou teplotou topenia, ako je oceľ alebo meď.
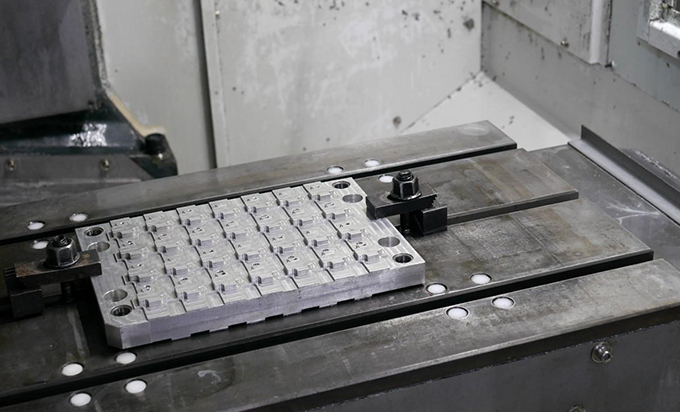
7.Extrúzia:
Extrúzia je proces, pri ktorom sa zahriaty kov tlačí cez matricu pomocou extrúzneho stroja, aby sa vytvorili súvislé tvary prierezu.Hlavné kroky zahŕňajú predhrievanie kovového bloku, extrúziu, chladenie a rezanie.
Výhody:
Efektívna výroba: Extrúzia je vhodná pre kontinuálnu výrobu, ktorá umožňuje rýchlu a efektívnu výrobu veľkých dĺžok a veľkého množstva dielov.
Všestranné tvary: Extrúzia sa môže použiť na výrobu rôznych tvarov prierezov, ako sú plné, duté a zložité profily, ktoré ponúkajú vysokú prispôsobivosť.
Úspora materiálu: Prostredníctvom kontroly tvaru a rozmerov vytláčacej hubice je možné minimalizovať odpad materiálu.
Nevýhody:
Obmedzená presnosť: V porovnaní s tlakovým liatím má extrúzia nižšiu presnosť a vyššiu drsnosť povrchu.
Obmedzenia materiálu: Extrúzia je vhodná predovšetkým pre kujné kovy ako hliník a meď.Pre tvrdšie kovy sa to stáva náročnejšie.
Výroba foriem: Výroba a údržba vytláčacích nástrojov si vyžaduje špecializované zručnosti a prináša vyššie náklady.
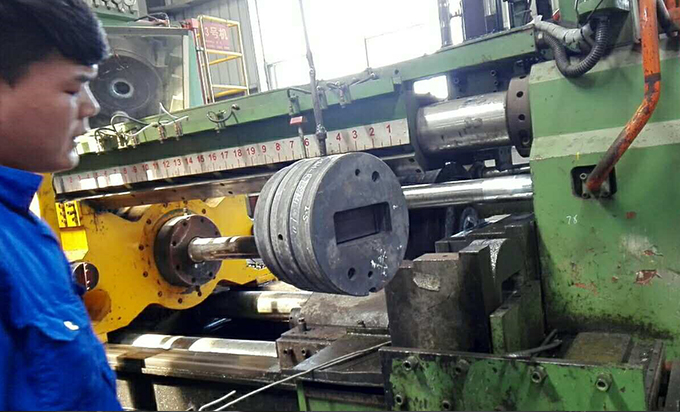
Ako si vybrať správnu metódu spracovania kovov na mieru
Dizajn produktu a požiadavky: Pochopte požiadavky na dizajn produktu vrátane požiadaviek na tvar, rozmery, materiál a povrch.Rôzne metódy spracovania kovov sú vhodné pre rôzne dizajny výrobkov a požiadavky.
Výber materiálu: Vyberte si vhodný kovový materiál na základe vlastností a požiadaviek produktu.Rôzne kovové materiály sú vhodné pre rôzne spôsoby spracovania.Napríklad hliníkové zliatiny sú vhodné na extrúziu a tlakové liatie, zatiaľ čo nehrdzavejúca oceľ je vhodná na CNC obrábanie a odlievanie.
Presnosť spracovania: Vyberte vhodnú metódu spracovania na základe požiadaviek na presnosť produktu.Niektoré metódy, ako napríklad CNC obrábanie a brúsenie, môžu poskytnúť vyššiu presnosť a kvalitu povrchu, ktoré sú vhodné pre produkty vyžadujúce vysokú presnosť.
Objem výroby a efektivita: Zvážte objem výroby a požiadavky na efektivitu produktu.Pre výrobu vo veľkom meradle môžu byť vhodnejšie vysoko účinné metódy spracovania, ako je razenie, vytláčanie a tlakové liatie.Pre malosériovú výrobu alebo produkty na mieru ponúkajú metódy ako CNC obrábanie a 3D tlač flexibilitu.
Úvahy o nákladoch: Zohľadnite nákladové faktory spôsobu spracovania vrátane investícií do zariadenia, toku procesov a nákladov na materiál.Rôzne metódy spracovania majú rôzne štruktúry nákladov, preto by sa mala zvážiť nákladová efektívnosť.
Náš tím profesionálnych inžinierov sa dobre orientuje v širokej škále metód spracovania kovov a môže vám poskytnúť cenné poznatky a odporúčania.Máme hlboké znalosti o najnovších pokrokoch v tomto odvetví a môžeme vám pomôcť zorientovať sa v zložitosti výberu najvhodnejšej metódy pre váš konkrétny projekt.
Či už potrebujete pomoc s presným obrábaním, kovaním, odlievaním alebo akoukoľvek inou technikou spracovania kovov, naši inžinieri vám môžu ponúknuť poradenstvo prispôsobené vašim požiadavkám.Zohľadníme faktory, ako sú vlastnosti materiálu, požadované tolerancie, objem výroby a úvahy o nákladoch, aby sme vám pomohli urobiť informované rozhodnutie.
Naši inžinieri vám navyše môžu poskytnúť podporu pri optimalizácii dizajnu vašich kovových komponentov z hľadiska vyrobiteľnosti, čím zaistia, že ich možno efektívne vyrábať pomocou zvolenej metódy spracovania.Môžeme ponúknuť návrhy na úpravy dizajnu, ktoré môžu zlepšiť celkovú kvalitu, funkčnosť a hospodárnosť vašich produktov.
Neváhajte ma kontaktovať a sme pripravení pomôcť vám dosiahnuť tie najlepšie výsledky pri obrábaní kovov.
Čas odoslania: 18. decembra 2023